I'm not going to describe how to measure the clearances. I'm assuming
here that you want to change the shims.
|
Thumbnail
(Click to see detailed photo) |
Comment |
1 |
|
Remove Fairing.
You need to remove the lower grey cowl and the middle fairing on both
sides. Get rid of the seat, and lift the tank as high as it will go
without removing the restraining cable. Secure it there. |
|
|
Remove Air filter Cover |
|
|
Remove Air Filter Housing Base
There are 8 Philips head bolts. On mine, the most inaccessible was
the one whos head stripped. You need a good screwdriver and a lot of
downward pressure to release the screws, and the petrol tank being in
the way of applying direct downward pressure doesn't help. The
stripped head problem was solved by tapping a slightly oversize
normal screwdriver blade into the least damaged part of the head.
There are two hoses - front and back - which are held in place with
circlips. Slide the circlip well down the tube before removing the
tubes and the housing, and remove the circlip afterwards to avoid any
chance of these stray bits of metal dropping inside any parts of the engine.
The butterfly valves on the throttle bodies act to prevent bits
falling into the combustion chamber, but plug them and cover them anyway. |
|
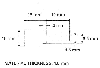 |
Tensioner
The manual describes a way of making a tool in order to release the
tensioner. Basically you need a piece of 1mm thick steel, about 15mm
wide. Grind down a blade 4.5mm wide and 19mm long. Grind down a
shoulder which is 3mm long and 8.5mm wide.
The measurements aren't that crucial as you can see from my version
of it. |
|
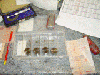 |
Shims
I removed both cam shafts from both sides and placed them into
plastic food bags with a slip of paper clearly labelling where each
had come from. I did the same with the cam plates and bolts. I kept
the valve followers and shims in the engine until I was ready, then
dealt with four at a time, placing followers and shims in a plastic
screw box with separate compartments. Note the micrometer, the knife
with magnifying glass the pencil and planned spreadhseet with shim
measurements. The micrometer is needed for measuring shims. i) You
can't always read the printed value, ii) the indicated measurement
doesn't always match the shim's thickness. My spreadsheet for metric
calculations will appear here. |
|
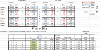 |
Link to a valve shim calculator - metric / imperial
There are plenty of them out there, this one is a little
different and allows you to play around with tolerances. More
details from the link - click the picture or choose 'Shim Calculator'
from the right hand menu. Metric and Imperial versions available.
Excel 2007 format. |
|
|
Molybdenum Disulphide Oil.
I can't find a source for this in the UK, but then if you read the
earlier sections of the service manual, it says to make it yourself
with Moybdenum Disulphide and Engine Oil - mixed 1:1. I used the Moly
60 paste (for the rear wheel splines) and engine oil, but I felt 1:1
was too thick, and added about 30% more engine oil. I didn't want a
paste that would clog up the lubrication holes in the camshaft. You
need this to provide lubrication for the camshaft before the oil gets
flowing around the engine again when you first start up. |
|
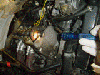
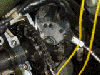 |
Right Hand Cam - replacing.
Put the timing mark on T2. (rotate the crankshaft anticlockwise). You
will need a torch and a mirror and a third hand. Make sure that
cylinder 2 is at top dead centre.
Fit the exhaust cam shaft first. Make sure that the non tensioner
side of the cam chain is tight, and rest the cam shaft in its journal
bearings. Check the timing marks. The 'R-Ex' mark should line up with
the top of the case.
The photo on the left shows one way of overcoming the parallax
effect, where if you do not look straight on, you can convince
yourself that you are a tooth out. Use a torch to project a shadow
onto the timing marks.
The 2nd photo shows the use of a mirror to establish that the
position of the inlet cam is correct. The 'R-In' mark should face outwards.
The yellow electrical cable is there to stop the chain falling into
the crankcase.
Take a look at the path of the chain inside the
crankcase. It is possible for the chain to have dropped to the wrong
side of the end of a shaft which protrudes. Use a long, clean
screwdriver to help manoeuvre it back into position.
Also, if you have been turning the engine with the
camshafts out, it is possible for the slack cam chains to have
slipped off the driving sprocket. When you pick up the chain again,
the chain does not wrap around the sprocket properly. Instead, there
is an unseen loop under the sprocket, which results in the chain
being too tight for the second cam to be located. If either of these
happen, re-check the timing mark on the first cam shaft before
proceeding to place the second cam shaft. |
|
|
Cam Covers - replacing
Lubricate the journals and lobes with your MoS2 oil.
Refit the Right hand cover. The 4 longer bolts have copper sealing
washers, which the manual says, should be replaced. It seems to say
that the bolts should be renewed too. The longer bolts are for the
four inner holes.
Fit the journal cover too - 4 bolts. Mine was difficult to locate by
hand, but went on very easily with the downward pressure exherted by
finger tightening the bolts.
Check the clearances.
Make sure the cam chain for the left hand side can move freely, and
cannot fall into the crank case and gently turn the engine over with
the ratchet (counter clockwise) a couple of times. Return to T1 and
check clearances again. |
|
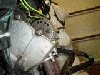 |
Left hand Cam Shaft
The timing mark should be at T1 with cylinder 1 at top dead centre.
Place the inlet cam first keep the non tensioner side of the chain
tight when placing the inlet cam. Get it approximately correct, then
adjust the chain cam one sprocket tooth at a time. Click the picture
for shots showing how to read / misread the timing marks. |